As part of our solution presentation, we will also examine your processes and requirements, discuss the benefits for your plants and answer your questions about the process industry APS solution.
Over 5,000 customers worldwide have already implemented Opcenter APS (formerly Preactor APS). As a partner company of Siemens Digital Industries Software with a team of 25 Opcenter experts, we offer you the competence centre for production planning in the process industry with Opcenter APS.

How to Achieve a Return on Investment
Up to
More Productivity
Up to
Less Inventory
Up to
Less Truck Downtime
Up to
Fewer Delays
Your Challenges in Production Planning for Continuous Processes
You can significantly reduce these cost drivers with our production planning solution for the building materials industry.
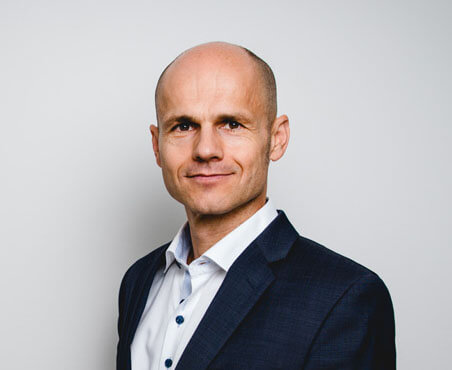
Christian Stiefsohn
Production planning in the building materials industry is more difficult than in other industries due to the need to forecast batch sizes, production, transport routes and the availability of container capacity. With our new process, planners can plan ahead, optimise and stabilise production. Several times a day, in line with changes in the order situation and events in production.
With Our Production Planning Solution, You Can Bring a New Level of Quality to Your Processes.
Book Your Individual Solution Presentation:
Production Planning for Building Materials
We would be happy to provide you with a complete overview of the solution and its applicability in your factory:
- Production processes and framework conditions
- Influential cost factors
- Detailed functional scope and mode of operation
- Process quality and reliability
- Solution architecture
- Methodology Implementation
- References
As part of our solution presentation, we will also examine your processes and requirements, discuss the benefits for your plants and answer your questions about the process industry APS solution.
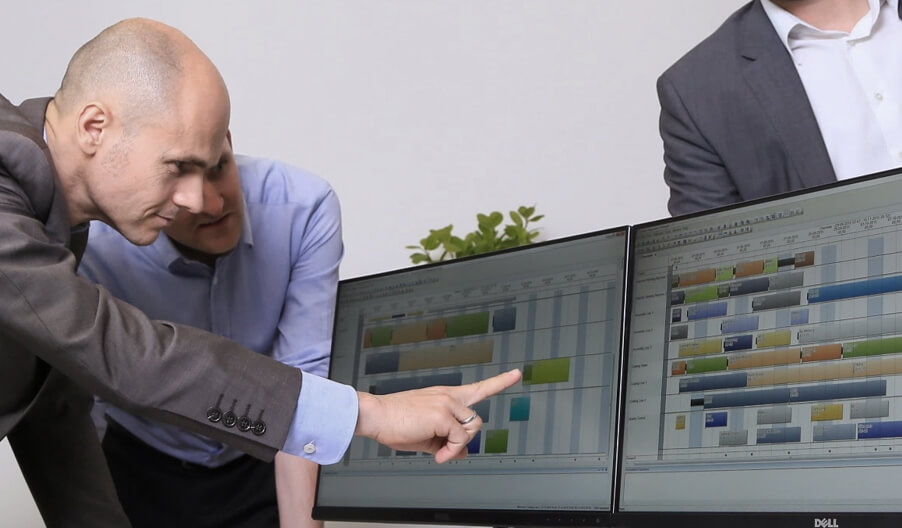
Success Story: Production Planning in the Mixed Feed Industry
Our operations managers used to calculate the production plan manually for all incoming orders, including silo occupancy, rinse batches, contamination matrix, etc. Today, we press a button and within two minutes we have a plan for all systems that includes everything we need for optimal plant operation.
The feed producer GARANT-Tiernahrung GmbH, market leader in Austria, has digitised its production planning with MCP Algorithm Factory. This has enabled the market leader in Austria to increase its efficiency in production, logistics and order management. Garant now saves many hours of work for key personnel every day; this time is being invested in the next important improvement projects to achieve the annual productivity targets. In this way, Garant is further expanding its leading role in the market.
Learn more about the solution used, the project and the goals that GARANT achieved with the implementation of our production planning solution for the mixed feed industry in the success story.
What Changes for Planners?

The Initial Situation at the Plant
When planning continuous processes, it is often impossible to predict which routes and silo capacities will be available. This means that planners have no chance of avoiding planning errors. These errors cost productivity and adherence to deadlines.
Planners devote almost all their energy to the next few hours in order to meet critical deadlines. One symptom of this situation is the frequent rescheduling of finished goods shortly before the delivery date because the wrong orders were prioritised.
Our New Process Enables You To:
- Reliably determine the production sequence for several days in advance
- Optimise the sequence
- Know the fill levels of containers in advance
- Determine a new production plan in just one minute due to disruptions or new orders