Our solution for production planning
In our non-binding potential discussion, we look at your processes and requirements, discuss the sensible use of software-supported planning and answer your questions about the implementation and operation of the compound feed APS solution.
Over 5,000 customers worldwide have already implemented Opcenter APS (formerly Preactor APS). We offer the implementation of this tool with a team of 15 experienced APS experts. We have a dedicated team for the compound feed/premixes sector.

How to achieve your ROI on investment
with Opcenter APS (formerly Preactor APS)
up to
more productivity
up to
less stock
up to
less truck downtime
up to
less delays
up to
better customer service: answer enquiries faster and more reliably than the competition
What can the compound feed & premix APS do?
Core functionality:
- Generation of production orders for unmet demand and stock items
- Calculation of the optimum batch size
- Assignment of work processes to mixers, presses and other ressources
- Sequencing of the selected ressources
- Calculation of silo and cell occupancy
- Calculation of transport routes
- Calculation of necessary stock transfers
Further functionality of the compound feed & premix APS:
- Consideration of the availability of raw materials
- Consideration of the availability of personnel
- Consideration of delivery dates
- Precise checking of the deadline dependencies of the process sequence
- Continuous filling of the press pre-cells
- Determination of process times from past production data (learning system)
- Minimisation of rinsing batches based on the contamination matrix
- Minimisation of set-up times and waiting times
- Consideration of different batch sizes for production and packaging orders (relevant for premixes)
- Filling of underloads through stock orders
- Graphic display of the entire planning horizon with highlighting of delays
- Display of the silo fill level over the time axis
- Personnel deployment planning at name level (add-on)
- Modelling of all necessary master data such as silo sizes, min/max of batch sizes, conversion of volume and weight, etc.
- Evaluations of call-off behaviour, truck on-time delivery and other key figures from the actual process (Excel solution)
Your challenges in the production planning of compound feed & premixes
You can significantly reduce these cost drivers with our production planning solution for the animal feed industry
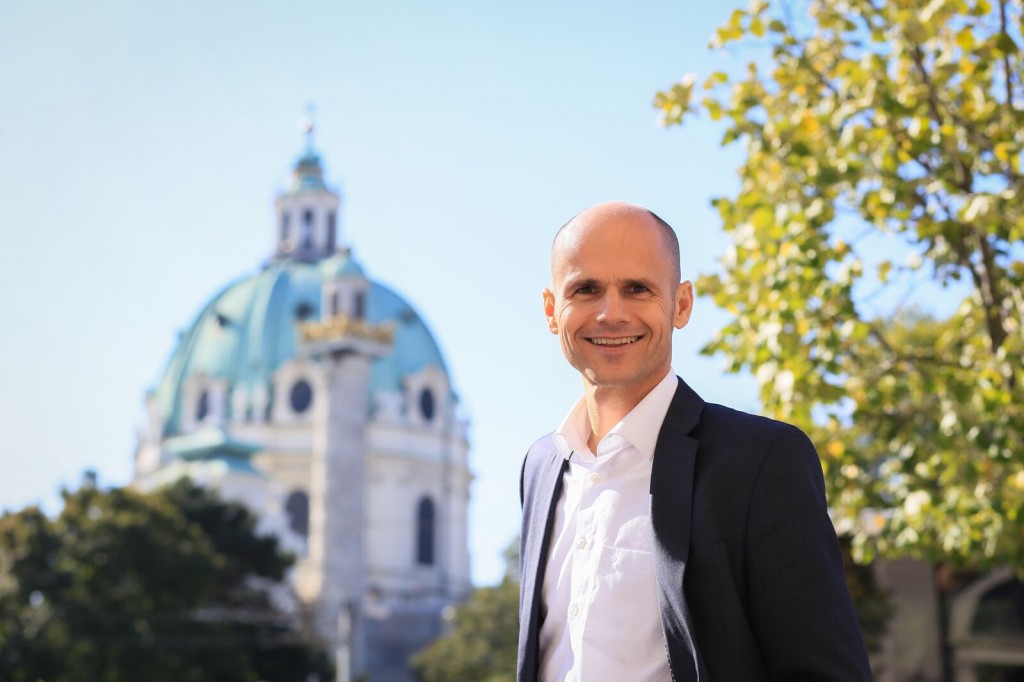
Christian Stiefsohn
Planning a feed factory is very difficult compared to other industries due to the need to anticipate batch sizes, production, transport routes and the availability of container capacity. With the feed APS, the planner can plan ahead, optimise and calm production. Several times a day, in time with the changing order situation and what is happening in production.
With the production planning solution in the animal feed industry, you can bring a new level of quality to your processes
Your first steps to success
We offer the following two web meetings to get to know each other. You are free to choose the sequence:
Let our experts advise you without obligation and secure your competitive advantage with the production planning tool.
In our non-binding potential discussion, we look at your processes and requirements, discuss the sensible use of software-supported planning and answer your questions about the implementation and operation of the compound feed APS solution.
If you would like to find out more afterwards, we recommend a slightly longer web meeting to give you a complete picture of the planning tool and its applicability for your factory:
Detailed solution presentation:
- Production processes and framework conditions
- Influenceable cost factors
- Detailed functional scope and mode of operation
- Process quality and reliability
- Solution architecture
- Implementation methodology
- References
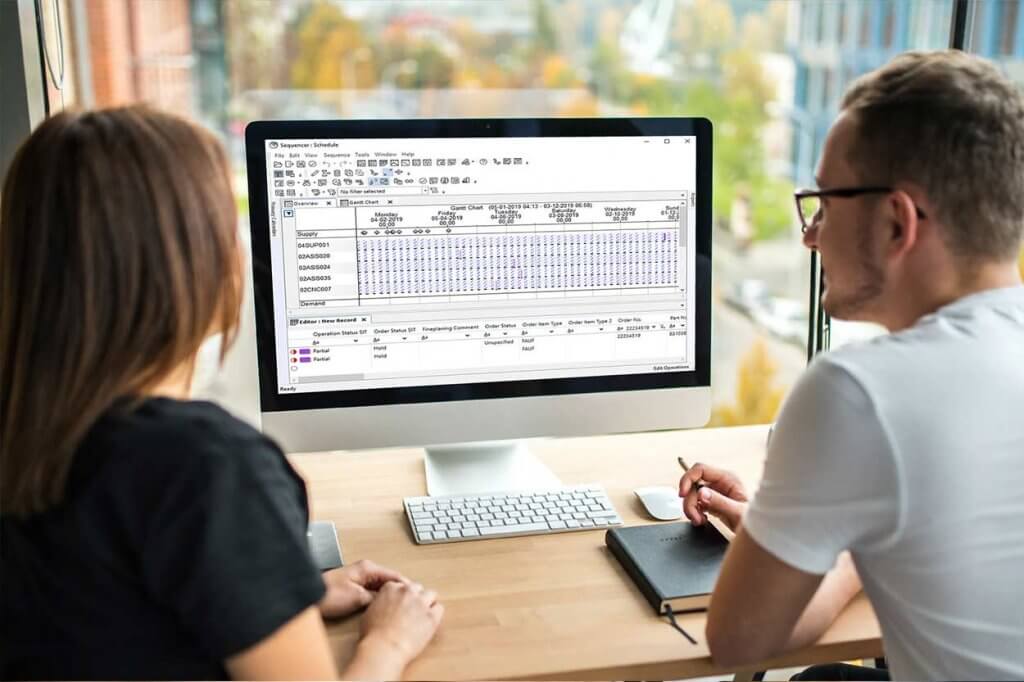
Success Story: Production planning in the compound feed industry
Our plant managers used to manually calculate the production plan for all incoming orders: with silo allocation, rinsing batches, contamination matrix… Today, we press a button and in two minutes we have a plan for all systems that contains everything we need to optimise plant operation.
The feed producer GARANT-Tiernahrung GmbH, market leader in Austria, has digitalised its production planning with MCP Algorithm Factory. This has enabled the market leader in Austria to increase its efficiency in production, logistics and order management. Garant is now saving many hours of effort from key personnel every day; this time is being channelled into the next important improvement projects to achieve the annual productivity targets. Garant is thus further expanding its leading role in the market.
Find out more about the solution used, the project and the goals that GARANT achieved with the implementation of our production planning solution for the compound feed industry in the success story.
What is changing for the planner?

The workplace in the established structure
The planner spends a large amount of time on recurring manual tasks during planning. Every time the plan is changed, silos, cells, transport routes and rinsing batches or the contamination matrix must be checked.
Although all details of the plan cannot be calculated for the entire order status, all orders must be delivered on time if possible. The planner must therefore find solutions to unforeseeable problems several times a day, such as the use of material for another order and its subsequent production.
The workplace with modern tools
The compound feed APS automatically takes into account all the details of production planning. Its algorithms are customised for the production processes and infrastructure in a compound feed/premix plant.
At the touch of a button, the planner can generate a plan that automatically makes all decisions, right down to the choice of loading cell. This eliminates the competing influences of planners and lorry dispatchers and provides an optimal plan for all parties involved.
In the event of any significant disruption and for planning new call-offs (“tour dates”), the planner effortlessly creates a new and optimised plan for the entire factory, i.e. several times a day.