
Get some no-strings advice from our experts and get a head start on the competition with our production planning tool.
In our no-obligation webinar, we will show you trends in production planning, present the state-of-the-art Preactor planning tool and clarify whether the application of the software tool is suitable for your individual needs.
MCP offers a customised planning and scheduling tool based on Opcenter APS (formerly Preactor APS) for all workstations in electronics manufacturing (SMD and THT).
Over 5,000 customers worldwide have already implemented Opcenter APS (formerly Preactor APS). With a team of 25 experts, we offer you the centre of excellence for production planning in the electronics industry.
Our Customers Achieve Their Desired ROI After Just a Few Weeks or Months.

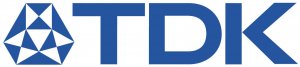
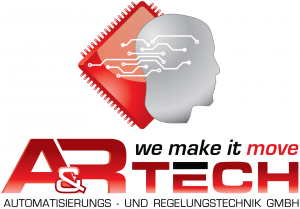
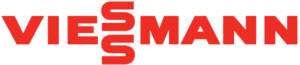

Other companies that use Opcenter APS for production planning in the electronics industry:
Your challenges in electronics production planning:
Siemens Numerical Control develops and manufactures numerical control systems for international markets. SNC faces challenges in the form of a high level of product diversity and complexity and rapid growth in production demand. Customers expect shorter lead times for deliveries, and SNC has a high inventory in its workshop. Watch the video to find out how they are overcoming these challenges with Opcenter APS (formerly SIMATIC IT Preactor APS).
Your Advantages With Our Production Planning Solution for Electronics With Opcenter APS (Formerly Preactor APS)
Our References: Opcenter APS (Formerly Preactor APS) at SUMIDA and TDK Electronics
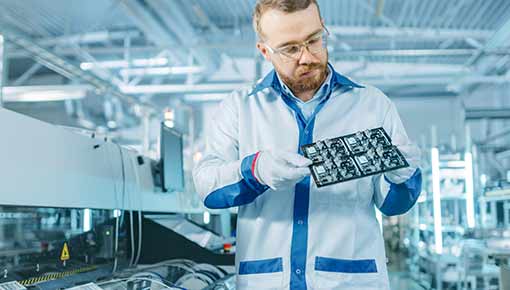

SUMIDA Lehesten GmbH is a global manufacturer of high-quality inductive components and modules. SUMIDA products are used in consumer goods, household appliances, automotive electronics, renewable energies, industrial electronics and medical devices.
SUMIDA has improved its production planning with MCP through intelligent algorithms and optimised planning processes. The key figures speak for themselves: delivery reliability increased from 62% to 98%, and production lead time (makespan) reduced by 35%.
Opcenter APS has enabled us to significantly increase our adherence to delivery dates and profitability. Our production planning is now a real competitive advantage.
Markus Herckner, SUMIDA Lehesten
Read our success story now about designing electronics production planning with Opcenter APS at SUMIDA.
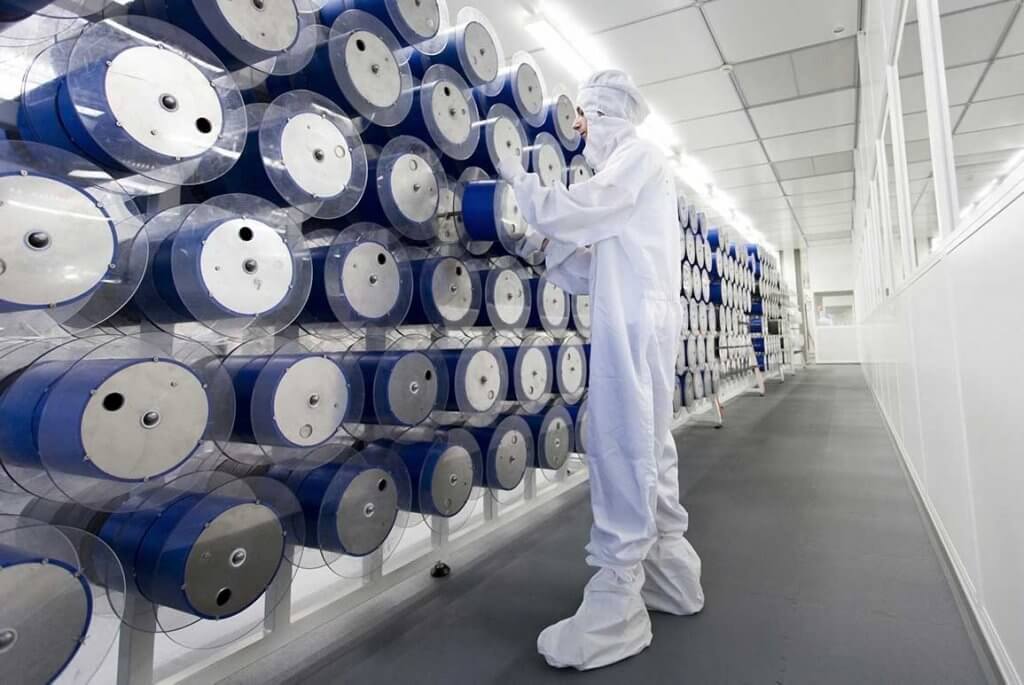
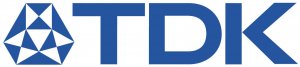
TDK Electronics, a subsidiary of the TDK Group, is a leading global supplier of electronic components and systems with a focus on technologically demanding growth markets in the automotive, industrial and consumer electronics sectors, as well as information and telecommunications technology. With around 20 development and manufacturing sites in Asia, Europe, North and South America, TDK Electronics is a reliable partner for its customers.
With the existing detailed planning based on SAP, specific solutions or Excel lists, the increasing requirements cannot be met in the long term due to the high variety of variants and multiple capacity constraints (people, machines, materials, production aids). This is made even more difficult by short-term customer enquiries and the production of prototypes with planning times that are difficult to estimate, which repeatedly cause changes in the short-term planning horizon. Further automation of planning is intended to increasingly replace manual work steps here.
Read our success story now about the design of the electronics production planning solution with Opcenter APS at TDK Electronics.
Planning Architecture in Electronics Production Planning
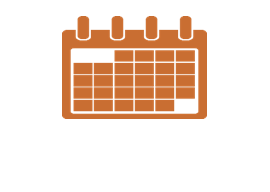
ROUGH PLANNING
- Long-term capacity planning for timely measures and capacity adjustments
- Fully automated planning for customers with a very high number of orders and high variability in the product mix
- Consideration of overlap between work steps: single-magazine flow
- Consideration of SMD setup families as a basis for setup optimisation within and between SMD lines
- SMT lines take setup families into account in order to provide a good basis for setup optimisation in the plant
- Control system for automatic splitting
- Alternative work plans: selection according to criteria
- Levelling of capacity utilisation and line allocation
- Advance planning: Personnel requirements, machine capacities, additional shifts, transfer to extended workbenches
- Quick response to delivery date enquiries and scenarios for ‘what if’ alternative scenarios
- Reduction of WIP and purchase line inventories
- Cascaded planning from rough planning at plant level to detailed planning in the individual production stages
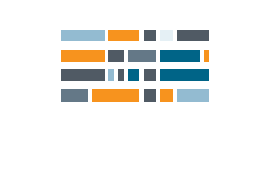
SCHEDULING
- Scheduling of individual work steps with start and end times, or simple forward/backward sequence planning
- Adjustable weighting of target criteria, e.g. balancing setup optimisation and adherence to deadlines
- Consideration of the critical ratio rule, e.g. for flat assemblies with highly variable process times
- For PCB assembly: Consideration of the sequence from SMT optimisation, from individual systems, from SetupCenter SiCluster sequencing or using VALOR across systems
- Assignment to workstations: Consideration of utilisation, capabilities, individual machines as favourites – also at article level
- Calculation of the exact process time depending on the batch size and the machine-dependent output per unit of time
- Ongoing adjustment and optimisation of the detailed plan in the event of system malfunctions
- Precise scheduling of high-priority requests in the near future
- Provision of information for automatic warehouse systems